28 - 31 October 2025 | Singapore Expo
Blog
Discover trending topics that are propelling the industry
Surface attraction at the finishing line
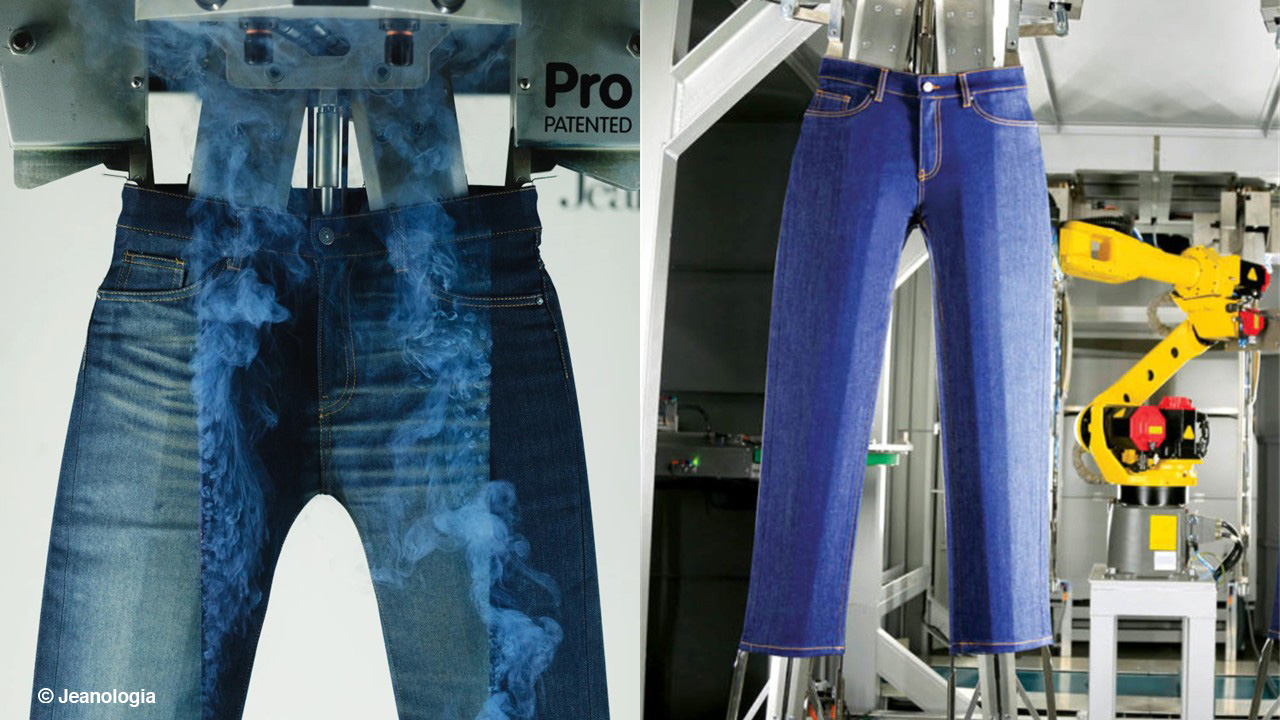
At ITMA Asia + CITME in Singapore from 28 to 31 October, visitors representing companies from the dyeing and finishing sector will discover many ways in which they can make major savings in dyestuffs and finishing chemicals, water and energy.
While sustainable practices are now a priority industry wide, investments in major new installations within the textile industry are based on cost projections based on many years of operation and will not be made again until absolutely necessary.
For this reason alone, a comprehensive sustainable transition will take time.
Spray advantages
It is, however, possible to make highly effective and practical adjustments to existing lines and spray finishing systems now represent a very cost-effective option.
A pioneer of this process is Baldwin, which is enjoying considerable success with its TexCoat G4 digital spray unit, which can replace traditional ‘padding’ or dip coating and other full immersion technologies to achieve significant savings in water, chemicals and energy.
This year, Baldwin has installed a TexCoat G4 on a Montex stenter range at the Monforts Advanced Technology Centre (ATC) in Mönchengladbach, Germany. The two companies are now collaborating with dye formulations specialist Archroma in full trials for many customers.
In third party testing, Fashion for Good, the platform for collaborative projects on sustainable textiles, has also made a comparison between TexCoat and padder-based finishing using a Monforts stenter and Archroma formulations. This has provided detailed data and confirmed that the intelligent combination of process know-how, equipment design and suitable chemistry significantly enables mill partners to reduce both energy and water use and also improves capacity utilisation.
With the TexCoat G4, 100% of the over sprayed chemistry is recycled and no chemistry is wasted during changeovers. Because only the necessary amount of chemistry is applied to the fabric in the first place, a reduced wet pick-up level of 50% can be achieved, cutting water and energy consumption in half.
Monforts has also introducing a range of modular upgrades that can be retrofitted to existing finishing lines already in production – all of which are aimed at further savings in energy, chemicals and water.
Double finishing
Denim jeans are meanwhile extensively finished twice – firstly as fabrics and then after being turned into finished garments – in processes that are largely unique to the sector.
Advanced denim laundries house a unique set of technologies that are used to create surface design effects on already cut and sewn garments.
When they leave the sewing factory, denim garments are stiff, deep indigo in colour and lacking the visual effects such as fading, whiskering or distressing that most consumers now associate with fashionable jeans. The laundry’s job is to simulate natural wear and tear, soften the fabric and sometimes adjust the sizing, shrinkage or colour tone.
Two of the latest technologies for achieving this are ozone fading and laser etching, both of which have been largely pioneered by ITMA exhibitors Jeanologia, headquartered in Valencia, Spain, and Tonello, of Sarcedo, Italy.
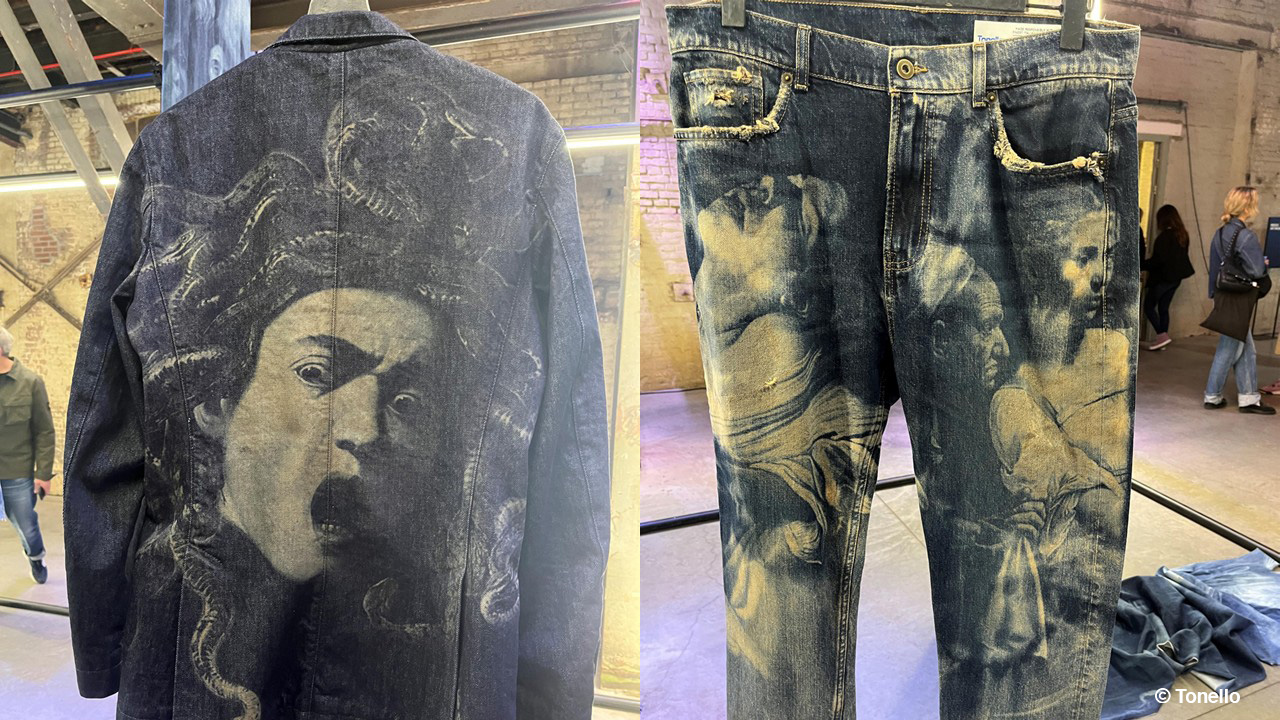
Ozone technology uses oxygen molecules to oxidise the dye on the fabric surface. The denim garments are placed in a closed chamber where ozone gas is introduced. The gas reacts with the indigo dye, lightening it to achieve various fade levels and wash-down effects.
This process drastically reduces water and chemical use with minimal energy consumption and no hazardous byproducts, since the ozone decomposes into oxygen.
Laser finishing
Lasers can meanwhile etch patterns such as whiskers, honeycombs or other fade lines onto the fabric with great precision and consistency to mimic the look of naturally aged jeans.
The high-energy lasers, guided by computer-controlled software, burn away the top layer of indigo dye on the fabric. The laser can be programmed to etch any pattern, from realistic wear zones to logos and complex graphics, allowing for mass customisation without the inconsistencies of manual labour.
Laser technology is being widely adopted by major denim brands and its hardware and software capabilities are being continuously improved.
Tonello’s Renaissance Collection has demonstrated the extraordinary detailing that is possible with modern laser technology, by replicating the designs of Italy’s Old Masters on denim garments.
Many more innovations for the advanced dyeing and finishing of fabric and apparel will be displayed in Singapore this October.